作者:姚遥
摘要
■ 投资逻辑
核心观点:锂金属负极较石墨、硅碳可实现更高的能量密度,为固态电池负极侧长期迭代方向;国内外企业已逐步应用锂金属负极方案,首款锂金属负极全固态电池已实现上车路测;工艺上,压延法率先实现规模化落地,向更薄迭代, 长期也建议关注蒸发镀、液相法;格局上,锂企、负极厂、箔材厂多方参与。建议积极布局各个工艺路线的领先企业。
锂金属负极:可实现更高的能量密度,为负极长期迭代方向。传统的负极材料石墨的循环性能好,但理论容量低;硅基负极理论容量高,但充放电过程中膨胀过大;锂金属拥有超高理论比容量和较低的电化学电位,根据欧阳明高院士,国内2030年前重点突破500Wh/kg电池,正负极侧主要依赖负极迭代,硅负极在助力电池能量密度突破400Wh/kg后的边际提升有限,锂金属负极已定性为负极侧长期迭代方向。
痛点:锂枝晶构成产品应用的主要瓶颈。锂金属的高活性和其表面SEI的锂离子扩散能垒较高会促进锂枝晶的形成,锂金属的不均匀沉积和枝晶生长会引发锂的体积膨胀、死锂产生、SEI破裂、极化电压增大、电池短路等问题,构成当前主要瓶颈,人工SEI膜、改性集流体、引入固态电解质是主要的改善锂枝晶的手段。
市场:国内外企业逐步应用,30年固态电池用锂金属出货有望达7700吨。当前大多数企业仍采用更为成熟的硅碳负极,海外日产、LG、SK On、Solid Power、Factorial Energy,国内宁德时代、清陶能源等逐步应用锂金属负极方案,今年初全球首款锂金属负极全固态电池上车(奔驰)路测。当前锂金属负极出货较少,我们假设2030年全固态电池出货180GWh,锂金属负极渗透率20%,采用双面20um锂箔,测算锂金属用量约7700吨,市场近百亿元。
工艺:压延法率先实现规模化落地,长期看关注蒸发镀、液相法。我们认为压延法率先实现规模化落地,但机械加工对于制备20um以下超薄锂带有所限制。长期看,5-6um是更为理想的锂层厚度,锂带过厚会导致锂的冗余,带来重量冗余,不利于能量密度的提升,也推高了成本。一方面,压延法仍有将锂带持续做薄的可能性,另一方面液相法、气相沉积法是潜在发展的方向,这两种工艺均可制备超薄锂带,但是离规模化量产仍有较大距离,气相沉积法在提升沉积速率、液相法在提高均匀性&提升铜锂浸润性上仍有较大迭代空间。
格局:锂企、负极厂、箔材厂多方参与,积极布局分工艺的领先企业。锂企如赣锋锂业、天齐锂业、天铁科技等,背靠丰富的锂资源和金属锂产能布局,在原材料金属锂锭的制备上具备成本、质量优势;负极厂如璞泰来、道氏技术(维权)、贝特瑞等同时在硅碳负极、锂金属负极上形成布局;箔材厂如中一科技、英联股份等也涉足锂金属负极。按工艺划分,天铁科技、赣锋锂业在压延法上领先,英联股份在蒸发镀上领先,道氏技术、中一科技等在液相法上领先。
风险提示
产业化不及预期、路线迭代风险。
+
目录
一、趋势:锂金属负极为负极长期迭代路线,锂枝晶问题待突破
1.1 锂金属负极为负极长期迭代路线
1.2 技术发展的痛点在于锂枝晶生长
二、工艺:压延法率先落地,长期可关注蒸发镀、液相法
2.1 挤压/压延法:当前最为成熟的工艺
2.2 蒸发镀&液相法:突破厚度瓶颈的新工艺
2.3 展望:压延法率先实现规模化落地,蒸发镀、液相法前景可期
三、格局:锂企、负极厂、箔材厂多方参与,压延工艺占当前主导
四、风险提示
正文
一、趋势:锂金属负极为负极长期迭代路线,锂枝晶问题待突破
1.1 锂金属负极为负极长期迭代路线
负极材料直接影响电池容量、首效、循环等性能。负极材料系先由负极活性物质、粘合剂和添加剂混合制成糊状均匀涂抹在铜箔两侧,再经干燥、滚压形成。负极材料作为锂电池不可或缺的重要组成部分,直接影响锂电池的容量、首次效率、循环等主要性能,在动力电池成本中占比一般不超过15%。
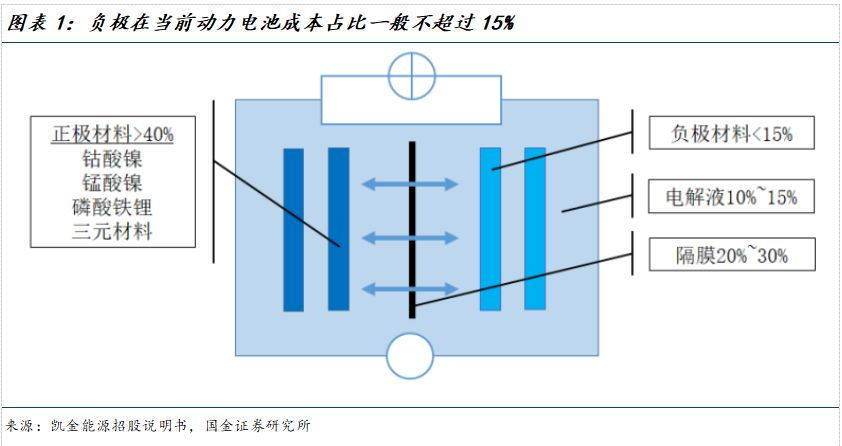
不同于传统石墨“脱锂-嵌锂”机制,锂金属负极主要通过“沉积-溶解”机制储能。根据工作原理,可将锂二次电池负极材料分为脱/嵌型负极、转换型负极、合金型负极及锂金属负极。脱/嵌型负极是指锂离子可在结构中发生可逆的嵌入和脱出的材料,如石墨等;转换型负极是指空间结构中不能提供锂离子脱/嵌位置,但可同锂发生转化反应的材料,如MnO2、CuO等;合金型负极是指能和锂发生合金化反应的金属及其合金、中间相化合物及复合物,包括硅等轻金属;锂金属负极是指直接以锂金属单质作为负极,锂离子在锂金属表面进行电沉积/溶解。
具体工作原理:
充电过程(锂沉积):外部电源施加电压,正极材料(如过渡金属氧化物)发生氧化反应,释放锂离子(Li⁺)。Li⁺通过电解质迁移至负极表面,同时电子(e⁻)经外电路流向负极。
反应式:Li⁺ + e⁻ → Li(锂离子在负极表面得电子还原为金属锂原子,沉积形成锂层)。
放电过程(锂溶解):锂金属负极中的锂原子失去电子,被氧化为Li⁺进入电解质,电子经外电路流向正极供电。
反应式:Li → Li⁺ + e⁻(锂原子溶解为离子)。
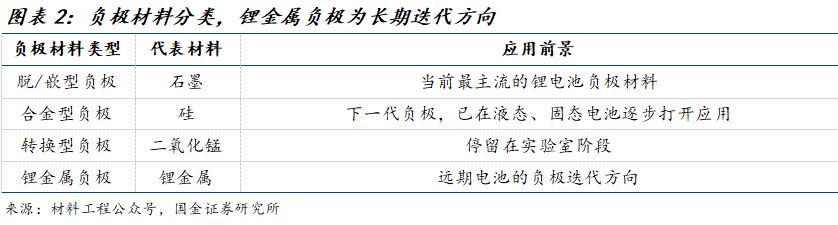
锂金属负极拥有高比容量和低电化学电位,可实现更高的能量密度。传统的负极材料石墨的循环性能好,但理论容量低;而硅基负极理论容量超高,但充放电过程中体积变化过大。不同于摇椅式锂离子电池的负极材料,锂金属拥有超高的理论比容量(3.86Ah/g),是石墨负极理论比容量(0.372Ah/g)的10倍以上,同时具有较低的电化学电位(-3.04Vvs.标准氢电极),因此被认为是最具潜力的负极材料之一。搭配过渡金属氧化物阴极,锂金属电池可以通过合适的电池体系设计达到400Wh/kg以上的能量密度。
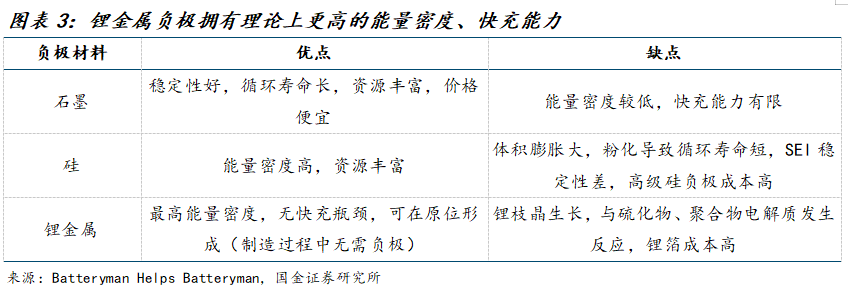
硅碳负极能量密度提升有限,锂金属负极为长期迭代方向。根据25年2月欧阳明高院士的发言,国内2030年前重点突破500Wh/kg以内电池,正负极方面三元正极不变,主要变负极。硅负极帮助电池能量密度达到400Wh/kg之前,随着自身克容量的增加,电池比容量几乎线性增加,而帮助电池能量密度达到400Wh/kg后,随着自身克容量的增长,电池比容量的边际增长明显缩小,而进一步突破能量密度上限仍需要依赖锂金属负极的应用。
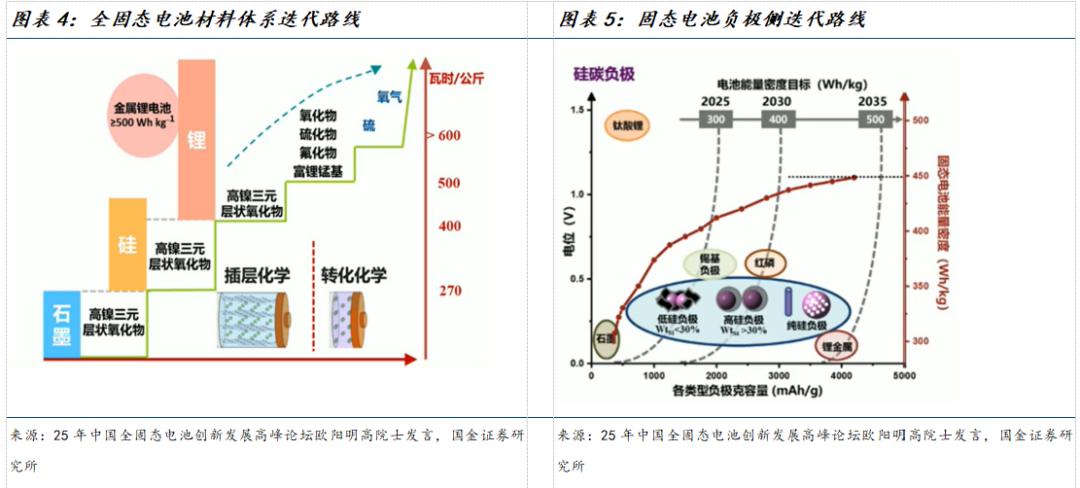
低硅→高硅→锂金属,负极发展路径清晰。根据欧阳明高院士,当前已行成已硫化物路线为主体的固态电池发展路线,根据正负极侧的迭代,具体的roadmap表现为:
石墨/低硅负极硫化物全固态电池(2025-2027):以200~300Wh/kg为目标,攻克硫化物固态电解质,打通全固态电池的技术链,三元正极和石墨/低硅负极基本不变,向长寿命大倍率方向发展。
高硅负极硫化物全固态电池(2027-2030):以400Wh/kg和800Wh/L为目标,重点攻关高容量硅碳负极,三元正极和硫化物固态电解质仍为主流材料体系,面向下一代乘用车电池。
锂负极硫化物全固态电池(2030+):以500Wh/kg和1000Wh/L为目标,重点攻关锂负极,逐步向复合电解质(主体电解质+补充电解质)、高电压高比容量正极发展(高镍、富锂、硫等)。
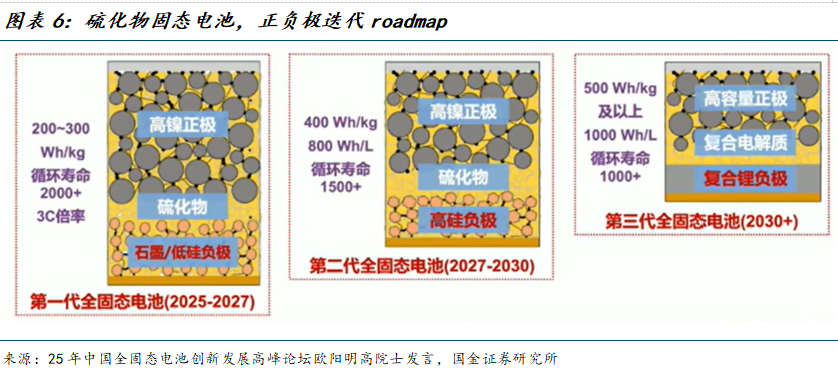
海外企业已有较多采用锂金属负极路线,国内固态电池企业负极侧尚以硅碳路线居多。海外日产、LG、SK On、Solid Power、Factorial Energy均采用锂金属负极路线,国内大多数企业仍采用硅碳负极,宁德时代、清陶能源、上海屹锂、恩力动力等采用锂金属负极。今年初奔驰应用锂金属负极的全固态电池上车路测,为全球第一款路测的锂金属负极电池。
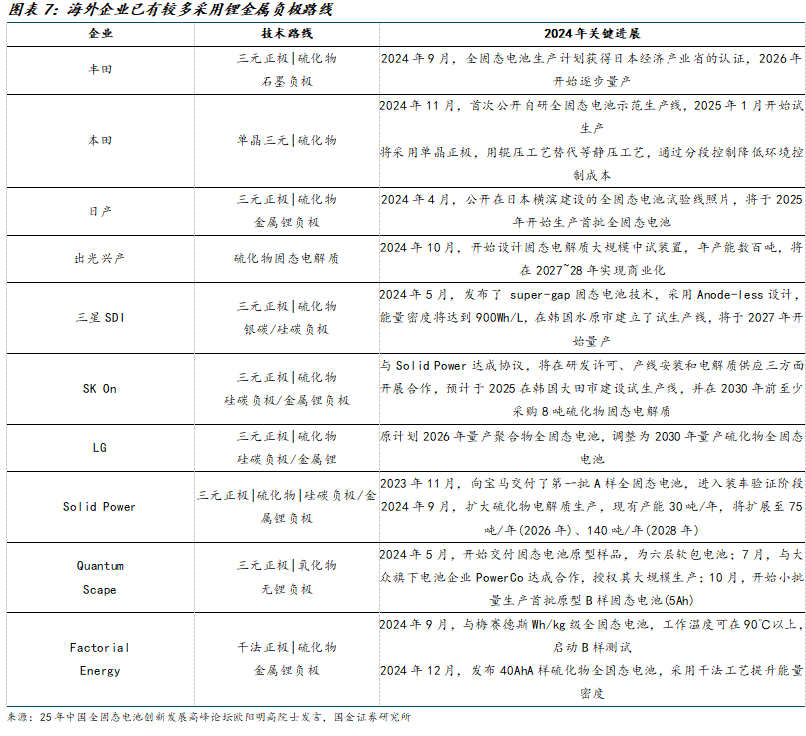
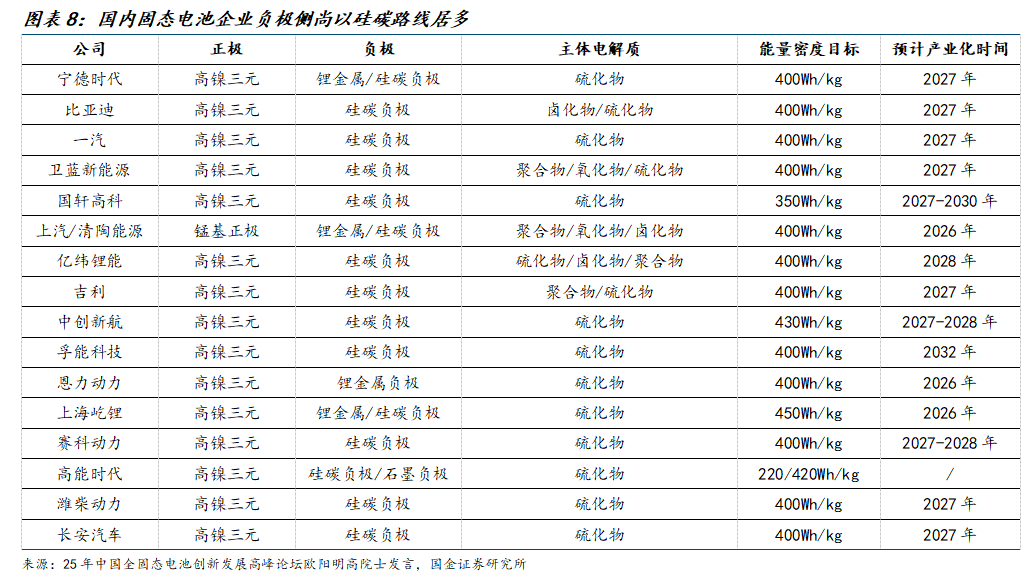
我们测算2030年固态电池用锂金属约7700吨,市场百亿。根据EVTank,2024年全球固态电池出货量达到5.3GWh,同比大幅增长4.3倍,全部为半固态电池,主要为中国企业生产。EV Tank预计全固态电池将在2027年实现小规模量产,到2030年将实现较大规模的出货。《中国固态电池行业发展白皮书(2025年)》预计到2030年全球固态电池出货量将达到614.1GWh,其中全固态的比例将接近30%。我们假设2030年全固态电池出货180GWh,锂金属负极假设渗透率20%,测算得36GWh。假设采用双面20um锂箔,合计40um厚度,1GWh电池用量1000万平,结合锂的密度534kg/m3,则对应1GWh电池用锂金属(不考虑铜箔)约214吨,18GWh对应用量约7700吨,假设120万元/吨,对应市场92亿元。
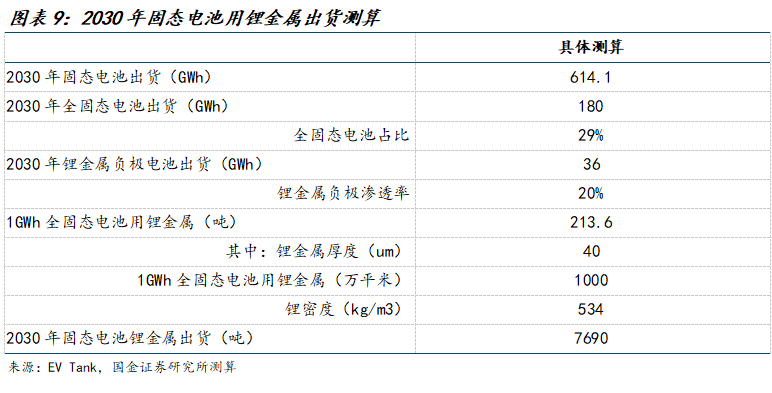
1.2 技术发展的痛点在于锂枝晶生长
锂金属的高活性和其表面SEI的锂离子扩散能垒较高会促进锂枝晶的形成。锂金属的不均匀沉积和枝晶生长会引发以下主要问题:
1)锂的无限体积膨胀:锂金属不同于石墨,硅等嵌入型或合金类负极,它是一种无基体转化型负极,石墨和硅的体积膨胀分别是10%和400%,而锂负极的体积膨胀是无限的,导致沉积锂的形貌结构呈现多孔疏松的状态。
2)死锂的产生:锂的无限体积膨胀和枝晶均会造成锂表面结构多孔疏松,经过多次充放电循环后,表面不稳定的锂会逐渐粉化并脱落下来从而失去电活性,从而产生大量死锂。
3)SEI破裂和副反应增加:锂枝晶的生长和死锂的产生会导致锂表面SEI破裂和重构,不断的重构SEI需要消耗额外的电解液,造成副反应增加。
4)极化电压增大:锂枝晶和死锂导致锂金属表面多孔疏松,SEI的比表面积和厚度均会随之增大,从而使Li+的扩散路径增加,并且死锂会导致表面阻抗增加,这些因素都会造成锂金属电池在多次循环 后的极化电压显著增加。
5)电池短路:锂枝晶的不断生长会造成其对隔膜的应力增加,最终会刺穿隔膜导致电池短路,从而引发电池热失控等安全问题。
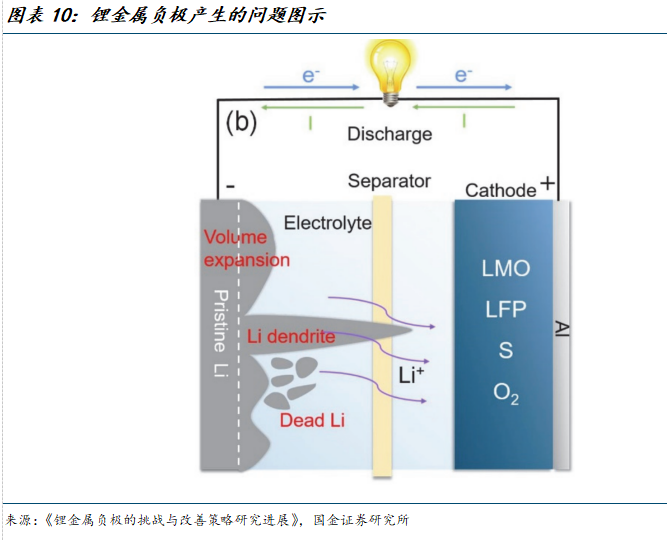
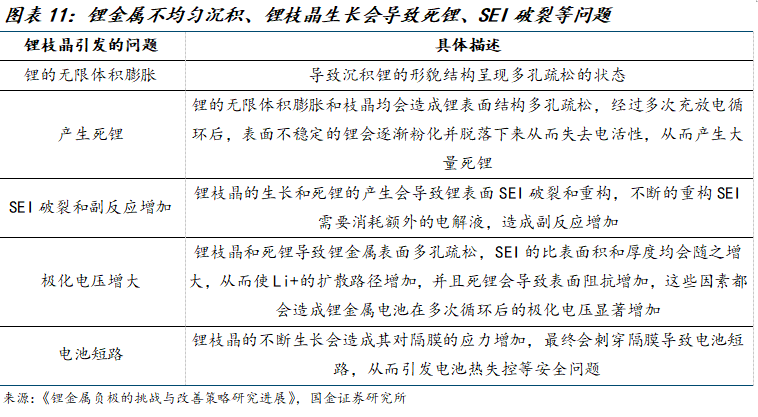
人工SEI膜、改性集流体、引入固态电解质是主要的改善锂枝晶的手段。改善锂负极的循环性能和安全性能策略主要包括:1)利用表界面调控策略,构建人工固态电解质界面(SEI)膜,引导锂的均匀沉积,缓解锂枝晶的危害;2)通过改性集流体或锂基底结构,构建复合锂金属电极,从而促进锂的均匀沉积;3)制备固态电解质或者准固态电解质,利用其力学性能抑制锂枝晶的生长及可能引发的短路问题等。
1) 构造人工SEI膜。
SEI膜反复破碎坍塌会造成电池失效。在锂电池的充放电循环中,负极表面会被覆盖一层钝化层,称为SEI膜,而稳定的SEI膜影响着电池的安全性、高低温性能、倍率性能、循环寿命、容量保持率和锂沉积的形态。一般情况下,SEI膜并不完全致密,且力学性能较差,在锂金属反复沉积和溶出过程中,SEI膜很易破碎或坍塌,导致新鲜的锂金属与电解液继续反应,形成新的SEI膜。这个过程被称为SEI膜的动态重构。如果SEI膜的破碎和坍塌过于频繁或失效,会导致锂电池容量衰减、安全性降低甚至失效,因此构筑稳定且离子扩散性能优良的SEI膜对提高锂电池的循环性能具有重要意义。
人工SEI膜为长期趋势。对SEI膜的性能调控主要有两种途径实现:①通过调节电解质添加剂的成分来调控形成的SEI膜的组分和结构;②构建人工SEI膜实现对锂金属的保护,进一步提升锂负极的稳定性和倍率性能等。前者的选择范围十分有限,因此人工SEI膜成为长期趋势。
良好的人工SEI膜应具有以下特点:①优异的离子导电性,保证Li+快速通过;②较高的机械强度,保证在界面循环过程中不破裂;③一定的弹性,缓解局部应力;④在电解液中具有高化学稳定性。
未来技术难点在于:①均匀性:确保人工构建的SEI膜在整个锂金属表面形成均匀、一致的覆盖,避免不均匀覆盖引发的问题,如局部电压失衡和锂枝晶形成;②多功能性:设计具有多功能性的人工SEI膜,既能防止电极与电解液之间的不良反应,又能促进锂离子传导和抑制锂枝晶生长,还能阻燃隔热提高电池的安全性。
通常来讲,由无机组分组成的薄膜对锂金属表现出优异的化学稳定性,但存在不连续和不均匀的缺陷;有机成分SEI膜多为聚合物等,聚合物相分布均匀,使Li+导电通道分布均匀,但其弹性模量低、机械强度较差。人工SEI膜的制备可通过不同的制膜工艺实现,包括硬模板法、溅射法、化学气相沉积法、旋涂法、滴涂法等。
2) 构建锂复合结构。
通过合理的结构设计能够均匀化电流密度,促进锂均匀沉积从而缓解循环过程中产生锂枝晶的危害,主要方法包括:①复合锂多维结构修饰;②元素掺杂;③制备富锂合金负极。
——复合锂多维结构修饰:在复合锂负极的结构优化中,将电极结构中集流体设计成三维结构或者特殊的多维结构,可以缓解锂金属体积变化过大导致稳定性差的问题。传统锂金属负极是平面或者其他二维结构,在多次锂沉积和剥离过程中体积会有巨大变化,使锂金属负极的结构发生明显变化。三维结构或者特殊的负极结构设计能很好解决这一问题。
——亲锂元素掺杂:从复合锂负极的组分入手,通过亲锂性元素的掺杂、添加亲锂涂层等,可以有效促进锂成核位点的均匀分布,从而提高复合锂负极的循环寿命。例如,引入亲锂元素Ag、Au、Al、Mg或N、P、F、O等,其在锂表面自发反应生成Li3N、LiNxOy、LiF等可降低锂成核的能垒,从而导致锂均匀沉积,明显了减少锂枝晶生成。
——合金类:由于锂金属的费米能级较低,富锂合金晶粒与Li+结合能高,可以为均相锂沉积提供丰富的亲锂位点。锂合金负极构建可以改善电池的充放电动力学,提高充电和放电速率,适应快速充电和高功率应用;可减少锂枝晶形成,降低电池内部短路的风险,提高电池的安全性;最重要的锂合金负极适用于多种锂金属电池体系,具有较好的适应性。因此,直接制备富锂合金也是改善锂负极循环性能和倍率性能的主要方法之一。制备富锂合金的方法主要有高温熔融法、高能球磨法、机械合金法、化学合成等。
3) 引入固态电解质。
利用固态电解质代替传统电解液是目前公认的解决锂枝晶问题最具前景的策略。对于与锂金属搭配的固态电池,通常要求固体电解质满足以下条件:高的离子电导率,1×10-3S/cm以上,以及低的电子电导率,1×10-9S/cm以下,保证电化学反应的稳定性,避免电池极化或短路问题;宽的电化学窗口,对锂金属具有良好的化学稳定性,同时抗氧化能力强,并更好地匹配高电压正极材料;高的离子迁移数,尽可能达到;良好的热稳定性,便于在不同温度下使用;高的机械强度,同时具有一定韧性,方便加工;低综合利用成本,利于大规模量产并用于电池制造;从生产到使用中绿色无污染,对环境友好。
二、工艺:压延法率先落地,长期可关注蒸发镀、液相法
2.1 挤压/压延法:当前最为成熟的工艺
挤压/压延法是一种简单、直接的锂箔制备技术。是机械加工手段,主要包括提锂、电解、挤压、压延工序。具体流程:从锂矿石(如锂辉石)或盐湖卤水中提取碳酸锂(Li₂CO₃)或氯化锂(LiCl),通过电解生产金属锂,锂锭通过挤压机形成条状,再经轧制机压延成所需厚度的箔片。
挤压/压延法是一种成熟的金属成型工艺。该工艺可用于锂金属的加工,一般该工艺可以将锂金属加工到250–400 µm,利用挤压工艺加工出的锂金属箔材具有良好的表面光洁度,但整体而言加工厚度的均匀性较差。仅仅通过挤压工艺生产的锂金属箔难以满足二次锂金属电池的需求,通常需要与其它工艺结合使用,如与辊压工艺配合,进一步是金属锂箔更加薄,表面更加均匀,目前使用辊压工艺可以将锂金属箔厚度降低至20µm,在辊压过程中为了克服锂金属强的粘附性,通常会添加一些添加剂来控制表面张力,保证在辊压后获得无损伤的锂金属薄膜。
压延法已可实现规模化的生产,但是在制备超薄锂带上有难度。锂金属的强度较低,制备薄(< 50 μm)、宽(> 100 mm)、长(> 10 m)的锂带时,挤压/压延法存在限制。一次性压延的锂箔存在厚度不均、断带和起皱等缺陷,针对于厚度低于 50 µm 的锂箔制备,工业上通常采用多次辊压的方法,并精确控制每次辊压的压缩比,严格调控压辊压力和速度能够提高锂箔的质量, 但也显著增加了生产成本。
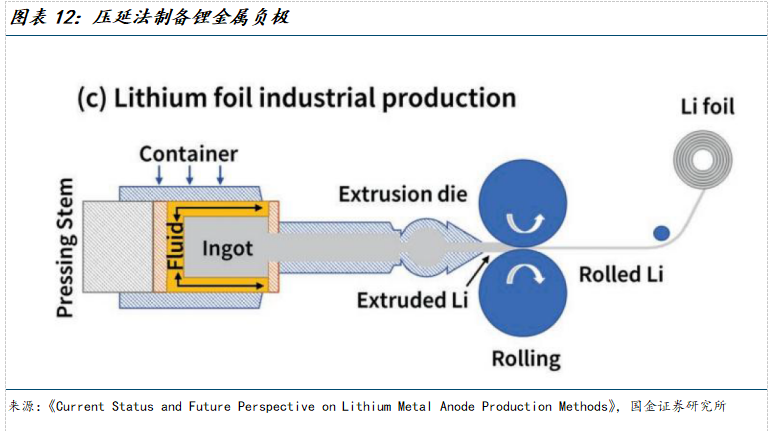
2.2 蒸发镀&液相法:突破厚度瓶颈的新工艺
1)电沉积方法:在集流体上电化学沉积锂金属,通过电解液中的锂离子还原形成锂层。
与辊压和熔融锂注入方法相比,电化学方法能够通过调控反应动力学和反应过程更精确地控制超薄锂负极的厚度. 电沉积是通过电化学过程将金属离子或络合离子还原为金属原子, 并附着于固体表面(导体或半导体), 从而形成金属层的过程. 采用电沉积制备金属锂箔(ED-Li)具有厚度可控、镀层均匀等优点. 可以解决锂金属由于在制造过程中受到大气污染, 表面覆盖的Li2CO3、LiOH 等组分的原生钝化层(NPL). 然而,电沉积技术仍处于发展阶段, 尚未成熟。
2)液相法(熔融法):基于锂相对较低的熔点,将锂熔融为液态后浸涂、喷涂或刮涂在其沉积在集流体上。
具体工艺为:将熔融状态下的锂金属均匀涂覆在导电支撑基材上,并使用压延机进行二次定型,这一过程不仅提高了锂与基材的结合强度,还能改善厚度均匀性,利用带有防粘涂层的冷辊能将锂箔厚度控制在10至50µm之间,有效解决薄层特性和均匀性问题。锂的熔融加工不仅可以在系统层面实现高能量密度,而且还为未来适应各种固态和液态电解质界面的后续原生表面工程提供机会。
熔融法的关键问题在于锂金属与铜集流体的浸润性较差,通常会在铜表面形成球状液滴,可以通过在基底上预涂有机过渡层,改善熔融态锂的浸润性,从而成功制备出多种小于50µm的超薄锂。例如:过渡层可采用氧化铜,当熔融锂与Cu2O层相互作用时,Cu2O被消耗,生成的Li2O和Cu不再以致密薄膜的形式存在,而是以嵌入锂金属的形式存在于 Cu 基材/锂涂层的界面区域,液态锂涂层在惰性氩气气氛下,采用卷对卷浸涂工艺进行制备,采用这种新工艺,锂厚度可在较大范围内调节(1-30 μm)。
该方法的劣势在于:①厚度不均:滴涂或注入可能导致厚度波动,影响电池一致性;②基体依赖:由于锂高表面能,其在各种相关基底上的润湿性较低,需亲锂涂层,否则锂渗透不充分,非活性基体会降低能量密度。
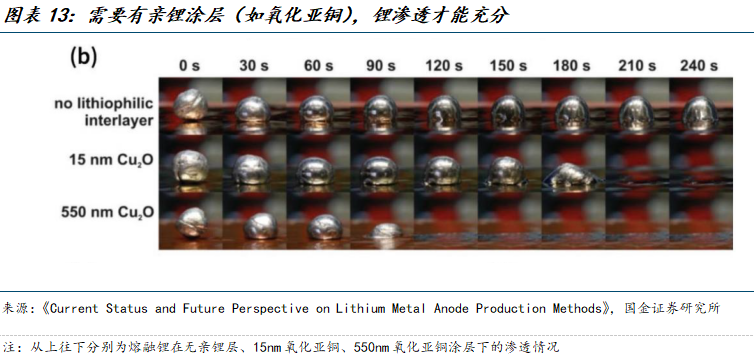
3)气相沉积法:利用物理气相沉积(PVD)技术在集流体上沉积薄层锂金属,其中蒸发镀最具备前景。
常见方法包括:
①蒸发镀:在真空环境中加热锂金属至蒸发,在铜箔上冷凝成薄膜。
蒸镀技术特别适用于低熔点和高蒸气压的材料,例如锂。蒸镀技术是沉积锂薄膜的首选方法,采用该方法为避免氧化,锂应保存在氩惰性气氛中并使用专用真空室进行锂沉积。热蒸发已被证明是获得金属锂薄膜最合适的技术之一,未来该技术可能会在金属锂二次电池生产中拥有一定市场地位,当前锂蒸发的研发和中试线级设备已实现商业化应用。如加拿大初创公司 Li Metal 正致力于将蒸镀技术用于金属锂箔的商业化生产。
通过调节蒸发温度,能够灵活控制所制备的锂离子薄膜厚度。这种物理减薄方法不仅实现了快速、连续的生产, 还具备了高精度的大规模生产能力。真空蒸镀技术提高了锂的利用率, 降低了锂的使用成本, 同时保障了负极的循环性能, 极大地提升了电池的综合性能。真空蒸镀技术为超薄锂负极的实际应用提供了一种可行的策略。
②溅射:通过大量电离出的氩气离子(Ar+)轰击靶材, 使靶材原子或分子被释放并均匀沉积到基片上, 无需高真空环境。
磁控溅射技术通过在基材上堆积金属锂原子, 可快速有效地制备出表面均匀平整、基材粘附性好和厚度在纳米或亚微米级的金属锂薄膜. 磁控溅射技术在薄膜电极材料[57]、人工SEI、隔膜等电池材料广泛使用。但由于制备过程的复杂性与高成本的制约, 磁控溅射无法大规模生产超薄锂箔。
③电子束物理气相沉积:通过电子束撞击目标并使锂金属靶材熔化或升华,将锂金属材料转变成蒸汽并沉积在基材的表面上。
EB-PVD主要优点是镀层杂质含量极低、沉积速率高、靶材喷射材料方向性好、材料利用效率高,短期内EB-PVD难以被用于锂金属箔材的生产。
④脉冲激光沉积:通过激光轰击锂靶材产生等离子体,沉积在基板上形成纳米级锂膜。在利用PLD技术时为了避免水的影响,通常需要在手套箱中操作以避免锂污染,使锂金属箔的制造成本较高,且不利于大面积金属薄膜生产。
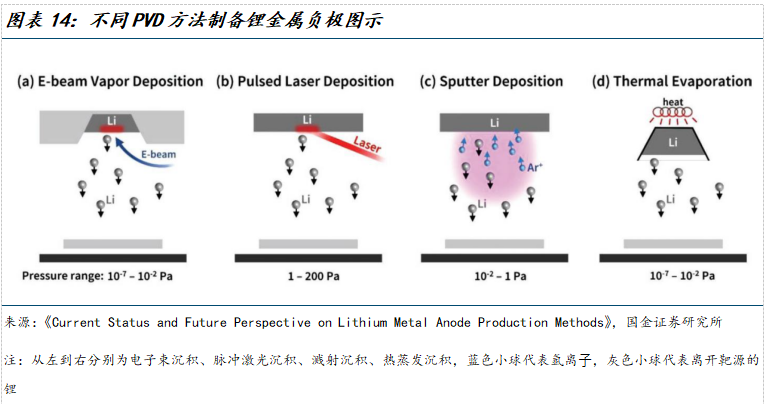
热蒸发是最优的沉积方式。溅射是一种广泛使用且工业认可的大区域沉积技术,但锂的低熔点(180.5°C)和对用作靶背板的铜等金属的缺乏粘附性使其不适合大规模锂加工。脉冲激光沉积(PLD)已被证明可以制造3微米厚的锂薄膜,但沉积时间很长(4小时,约8纳米/秒),且基底面积小(2平方厘米)。热蒸发(TE)可以利用低温下锂的低熔点和高蒸气压,沉积速度超过100纳米/秒,该技术在工业卷对卷(R2R)过程中已经非常成熟。与轧制的锂薄膜相比,使用TE生产的锂薄膜具有良好的均匀性和表面共形性,并且几乎没有缺陷。因此,热蒸发被认为是迄今为止最适合生产具有控制厚度、高质量和可重复性,并且可在工业规模生产的薄膜的技术。
根据能源学人和文章《Current Status and Future Perspective on Lithium Metal Anode Production Methods》,热蒸发(TE)可以利用低温下锂的低熔点和高蒸气压,沉积速度超过100纳米/秒,该技术在工业卷对卷(R2R)过程中已经非常成熟。与轧制的锂薄膜相比,通过蒸发镀制备的锂金属负极在表面均匀性和共形性方面表现出色,可实现无缺陷表面。同时,蒸发镀可以很好地控制锂层的厚度,其厚度范围可以从纳米到几十微米,因此有可能克服目前锂金属负极的厚度限制。目前,蒸发镀已用于生产薄膜电池的锂金属负极,蒸发锂的研发和中试生产线设备已实现商业化,加拿大公司Li Metal计划将蒸发锂工艺的锂金属负极商业化,其⼀条中试生产线已投入运营。
2.3 展望:压延法率先实现规模化落地,蒸发镀、液相法前景可期
1)技术程度上看,压延法>气相沉积法>液相法>电化学沉积。比较来看,压延法当前已经在固态电池领域得到了商业化应用,其成熟度最高;气相沉积法、液相法均处于量产验证阶段;电化学沉积处在实验室实验成功阶段。
2)加工性能上看,气相沉积法、液相法>压延法>电化学沉积。压延法当前可制备20um锂金属负极,具备生产高效、可量产优势,已有规模化应用,率先规模化落地,但是后续向超薄锂带(20um以下)突破有难度;气相沉积法、液相法均可以制备超薄锂金属负极,其中气相沉积法未来需解决沉积速率慢的痛点,而液相法需突破锂层均一性、亲锂层设计等工艺难点;电化学沉积法目前在锂上的应用仍较少。
3)经济性上看,液相法>压延法、电化学沉积法>气相沉积法。液相法的工艺相对简单,在经济性上具备较大前景;压延法具备较好经济性,能制备连续化薄卷,材料利用率好,有大规模生产能力,成本约1公斤250美元;电化学沉积法的工艺所需温度较低,降本有前景,但是连续化生产效率降低+电解质回收推高了整体成本;气相沉积法由于设备昂贵和真空密封,加工成本相对较高。
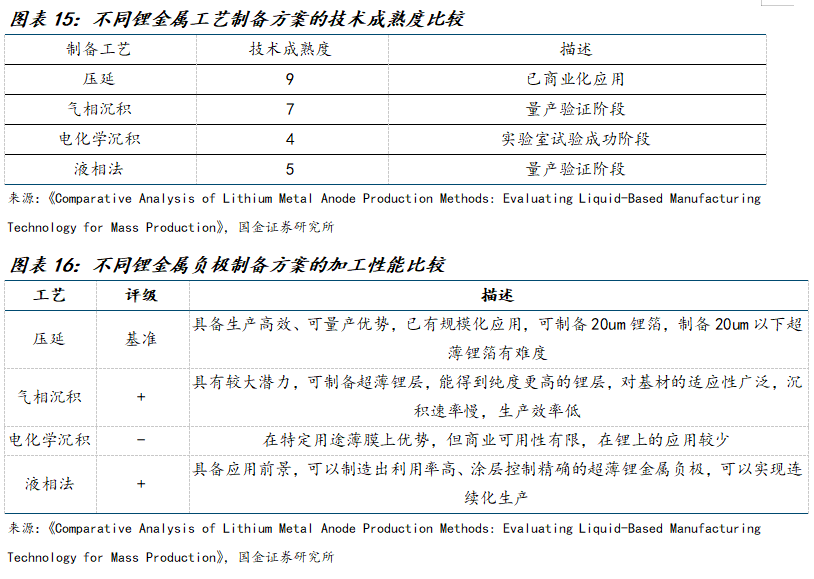
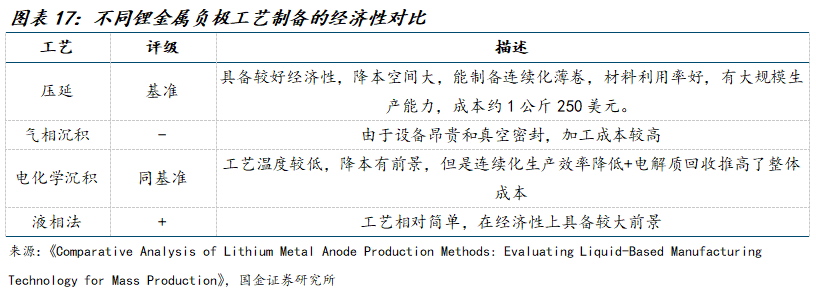
压延法率先实现规模化落地,长期看关注蒸发镀、液相法。将不同工艺做产品质量、工艺可行性的二维比较后,我们认为压延法率先实现规模化落地,但机械加工对于20um以下超薄锂带有所限制。长期看,5-6um是更为理想的锂层厚度,锂带过厚会导致锂的冗余,带来重量冗余,不利于能量密度的提升,也推高了成本。一方面,压延法仍有将锂带持续做薄的可能性,另一方面液相法、气相沉积法是潜在发展的方向,这两种工艺均可制备超薄锂带,但是离规模化量产仍有较大距离,气相沉积法在提升沉积速率、液相法在提高均匀性&提升铜锂浸润性上仍有较大迭代空间。
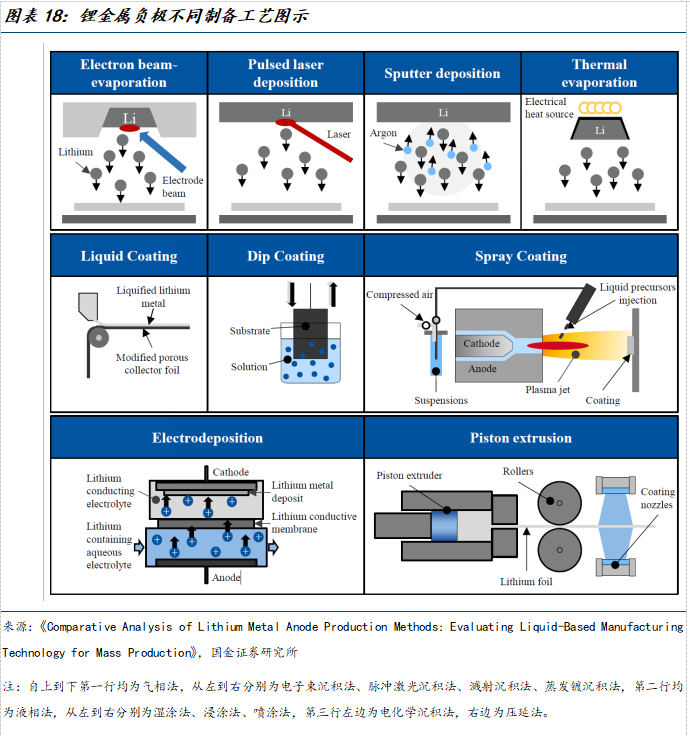
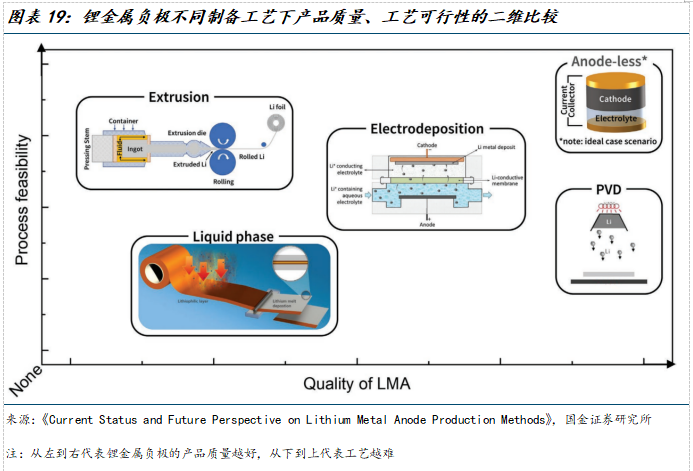
三、格局:锂企、负极厂、箔材厂多方参与,压延工艺占当前主导
锂企、负极厂、铜箔厂多方参与。锂企如赣锋锂业、天齐锂业、天铁科技等,主营业务为锂提炼加工,背靠丰富的锂资源和金属锂产能布局,在原材料金属锂锭的制备上具备成本、质量优势;负极厂如璞泰来、道氏技术、贝特瑞等同时在硅碳负极、锂金属负极上行成布局;箔材厂如中一科技、英联股份等也涉足锂金属负极。按工艺划分,赣锋锂业、天铁科技在压延法上领先,英联股份在蒸发镀上领先,道氏技术、中一科技等在液相法上领先。
1)锂企业:赣锋锂业、天齐锂业、天铁科技等。
赣锋锂业:行成负极端硅碳、锂金属双路线布局。
公司目前已实现300mm宽度的超宽幅超薄锂带量产,铜锂复合带中锂箔厚度可达到3微米。在电池及系统层面,赣锋320Wh/kg高比能电池,采用硅碳负极,循环可达到1000圈;400Wh/kg高比能电池,采用硅碳负极,循环达到600圈以上;500Wh/kg超高比能电池,采用锂金属负极,已实现10Ah级产品的小批量生产;集团具备完整设计能力,CTP成组效率达74%、生产效率提升30%。
天齐锂业:与卫蓝新能源合作预锂化、金属锂制备。
公司全资子公司天齐创锂与北京卫蓝新能源共同出资设立了合资公司深圳固锂,专注于预锂化负极材料、金属锂负极及锂基合金(复合)负极材料、预锂化试剂及相关制造设备等业务。目前,深圳固锂的预锂化实验室建设项目已竣工验收,并完成两套负极预锂化设备工艺开发及中高量预锂化设备第一阶段带料调试工作,其全资子公司天齐卫蓝固锂新材料(湖州)有限公司已掌握金属锂负极预锂化及金属锂负极制备的整套工艺与关键装备制造技术。
天铁科技:与欣界能源合作压延法锂金属负极。
公司在固态电池锂金属负极材料供应、研发、生产等方面全方位开展战略合作,实现双方优势互补,拓宽双方合作领域、提高合作层面,实现合作共赢。根据协议,双方将在固态锂金属负极材料产品供应、新材料研发、产线建设等方面展开深度合作。具体合作内容包括:天铁科技根据欣界能源的需求提供2款电池级锂金属产品供其进行样品检测;在样品检测合格且产品可满足需求的情况下,欣界能源在同等条件下优先向天铁科技采购金属锂负极材料产品,并在首条≥450Wh/kg固态2GWh量产线投产后,由天铁科技负责该条产线的金属锂材料供应,年采购量原则上不低于100吨,采购期限不少于5年;双方还将共同研发电池级锂金属负极材料,整合优质资源,加强协作,开展新型锂金属负极材料研发合作。
2)负极厂:包括道氏技术、璞泰来、贝特瑞等。
道氏技术:合作电子科大布局液相法锂金属负极。
公司与电子科技大学签署了《项目技术委托开发合同》,委托电子科技大学进行超薄金属锂负极的研发,包括单面/双面锂覆铜超薄锂负极带材的开发和自支撑超薄锂负极带材的开发,合作期限为2024年12月2日至2027年12月1日。
项目将由电子科技大学李晶泽教授负责实施,其团队由一支经验丰富、专业技能强的研究队伍组成。项目将通过利用高温熔融金属锂与金属集流体之间的相互作用,不仅改善二者之间的浸润性,通过熔融液体流延的方法实现锂负极的超薄化制备,而且借助金属锂与金属集流体之间的原位合金化反应,将原位生成的合金微纳网络结构作为三维骨架,克服传统纯金属锂负极体积变化大,且对锂的成核、生成缺乏约束的缺点,有效抑制锂枝晶生长,延长负极的循环寿命,大幅度提高其电化学性能及安全稳定性,加速包括固态锂电池在内的锂二次电池的商业化进程。
璞泰来:公司对锂金属负极材料持续研发,通过构建新型三维骨架结构来解决锂金属负极的枝晶、体积膨胀以及负极/固态电解质的界面问题,与此同时,公司锂金属负极成型设备采用压延复合工艺,已完成设备样机开发并交付使用。
贝特瑞:布局锂碳复合材料。通过对碳材料基体的精细设计及微孔结构调控,再通过现金的复合工艺将金属锂与碳材料复合,获得超高容量、低膨胀及长循环的锂碳复合材料。
3)箔材厂:包括英联股份、中一科技等。
英联股份:布局蒸镀法锂金属负极,合作头部车企。
公司在固态电池材料方面,依托蒸镀工艺的技术储备,研发锂金属/复合集流体负极一体化材料,并与头部汽车公司开展相关的技术合作,公司将会持续开拓复合集流体的应用场景。
中一科技:布局锂-铜金属一体化复合负极材料。
目前公司已有用于固态电池的锂-铜金属一体化复合负极材料等相关技术储备,可以改善金属锂与铜箔之间的界面亲和性,从而提高锂金属电池的循环稳定性。公司“一种锂-铜一体化复合负极材料及其制备方法和应用”的专利(公开号CN120048853A,申请日期为2025年03月),显示,本申请提供了一种锂-铜一体化复合负极材料及其制备方法和应用,属于电化学储能技术领域,其中,包括依次层叠设置的铜箔、锂合金层和碳层,锂合金层包括锂金属和亲锂金属,亲锂金属包括银、锌、锡、铝、镁中的至少一种,碳层由热还原处理后的碳材料制成。本申请通过在铜箔表面涂覆锂合金层和碳层,能够增强金属锂与铜箔之间的结合程度,减少了锂负极与铜箔之间的界面阻抗,有利于电子的传输,提供更高的导电性和更强的界面结合力;碳层具有较高的导电性和良好的锂离子传输能力,可以有效减少界面阻抗并抑制锂金属在铜基底上不均匀沉积,减少锂枝晶的形成。
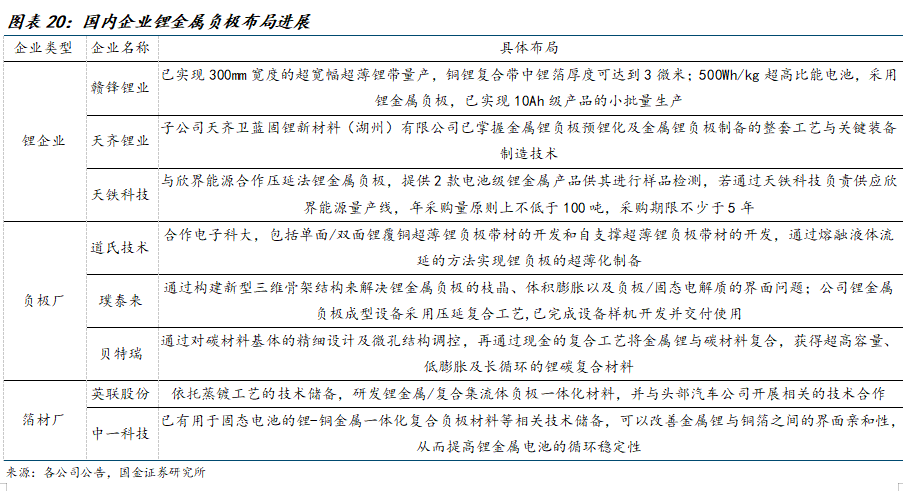
四、风险提示
产业化不及预期:锂金属工艺为固态电池负极的长期发展方向,工艺难度高,在固态电池上的产业化落地不确定性大,存在不及预期风险。
路线迭代风险:锂金属分多种工艺,当前看压延法占主流,蒸发镀、液相法为长期看仍有机会的新工艺,当前未到大规模商业化阶段,各工艺均有优劣,工艺路线尚未形成明确收敛,若未来伴随部分路线的痛点攻克,或者部分路线的痛点迟迟难以解决,将带来内部工艺路线的分化,部分行业内企业将受到冲击。
阅读全文
《锂金属负极:负极长期方向,关注各工艺领先企业——固态电池深度》 ]article_adlist-->+
报告信息
证券研究报告:《锂金属负极:负极长期方向,关注各工艺领先企业——固态电池深度》
报告日期:2025年07月04日
作者:
姚遥 SAC执业编号:S1130512080001
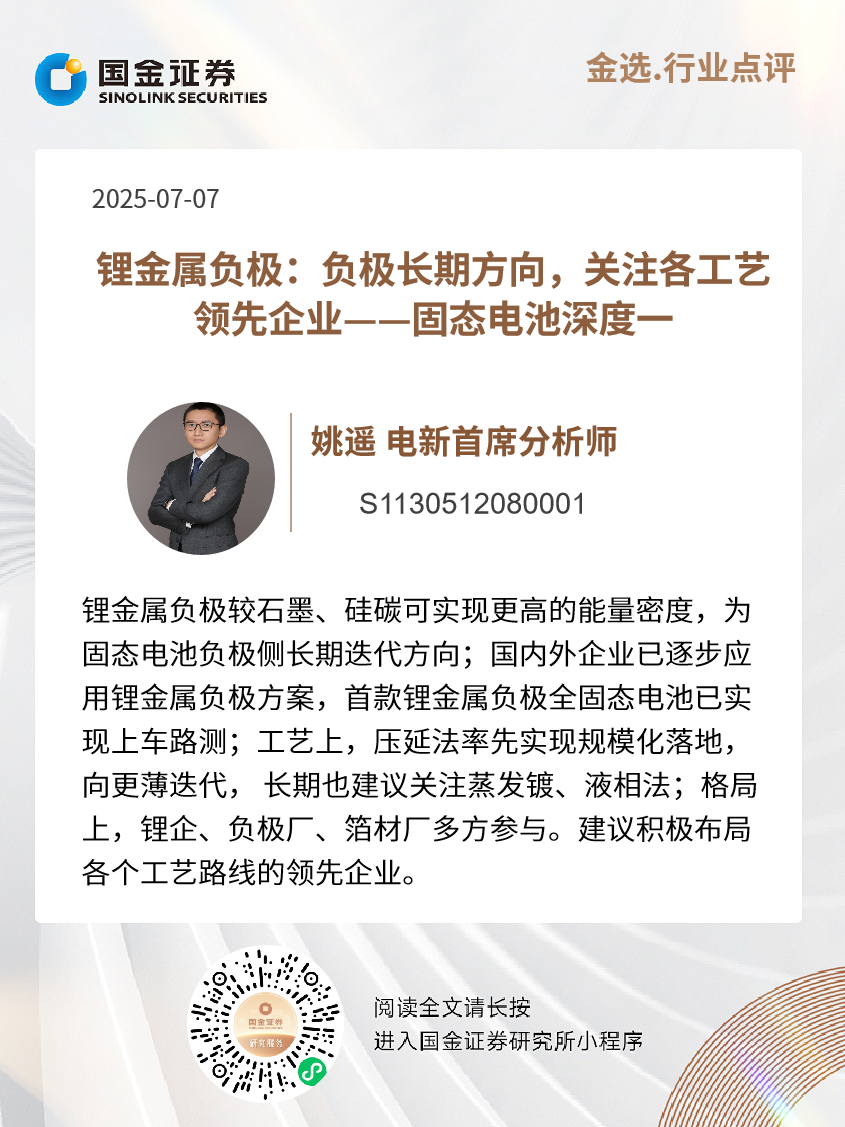
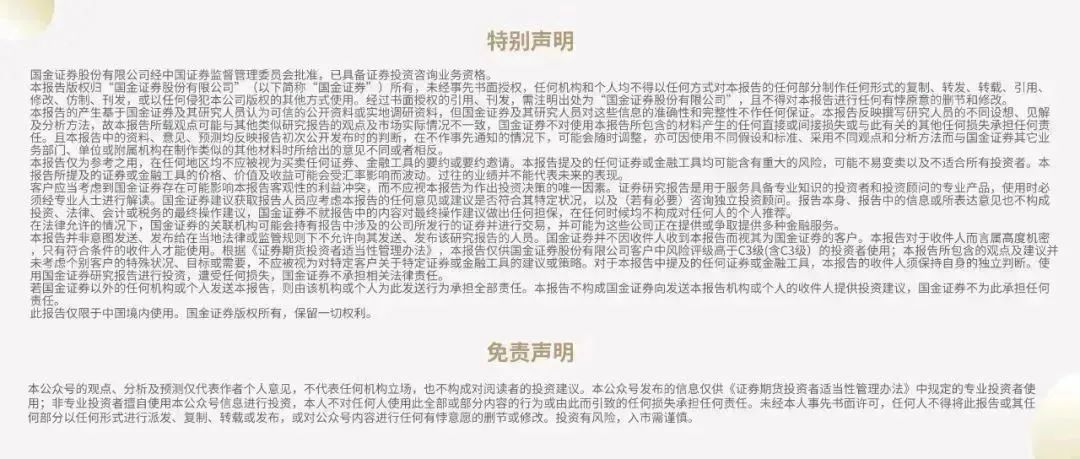
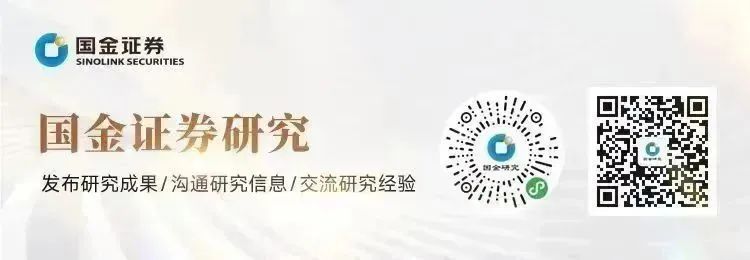
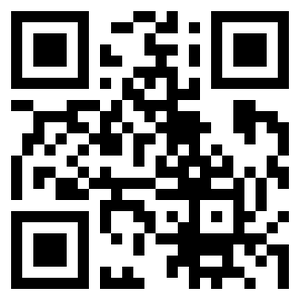